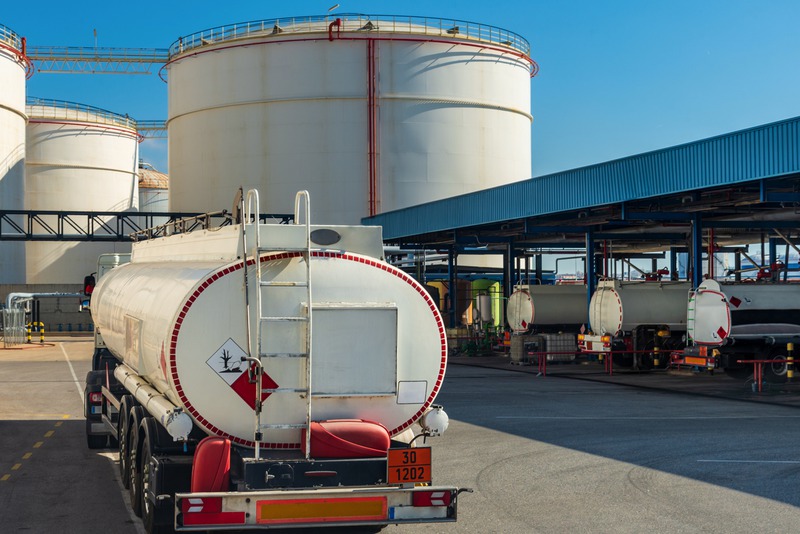
What Constitutes an Effective Oil Analysis Program?
An effective oil analysis program is a critical element in any proactive maintenance strategy for machinery and engines. It’s a procedure that assesses the health of oil and equipment to identify potential issues before they become major problems. In managing such a program, it’s essential to grasp the various aspects that lead to success, from sampling frequency to data interpretation.
Establishing Clear Objectives
Before diving into the specifics of oil analysis, setting clear goals is vital for ensuring that the outcomes support your maintenance objectives. Goals could range from extending oil drain intervals to improving equipment reliability. Without defined objectives, it’s challenging to measure the success of the program.
Sampling Consistency and Accuracy
For oil analysis to be effective, samples must be consistent and accurate. This involves using the correct techniques and tools for collecting oil samples, as well as adhering to a regular schedule that aligns with operating conditions and the objectives set.
Comprehensive Testing Parameters
Depending on the machinery and goals, a range of tests may be necessary. Key testing parameters often include:
-
Viscosity
-
Wear metals analysis
-
Contaminants detection
Each test provides insights into different aspects of the oil and equipment’s condition, helping identify issues such as contamination, wear, or oil degradation.
Effective Data Management and Interpretation
Data collected from oil analysis is only valuable if it’s well-managed and correctly interpreted. This requires both a robust software system to track trends over time and skilled personnel who can decipher what the data means for the equipment’s health and operation.
Working with a knowledgeable oil analysis program can provide the expertise needed to translate complex data into actionable insights for your maintenance team.
Actionable Reporting and Communication
The success of an oil analysis program hinges not only on the accurate testing of oil samples but also on the effective communication of the test results. The data gathered from oil analysis can provide insights into the health of the machinery and indicate when maintenance is needed. However, this information is only as good as the maintenance team’s ability to understand and act upon it. Therefore, it’s crucial that the results are presented in a clear, understandable format that allows maintenance personnel to make informed decisions and take timely, appropriate actions.
Actionable Reports
Report clarity is essential in oil analysis. The reports should highlight key findings and recommend specific actions, allowing maintenance staff to prioritize their tasks efficiently. These actions might range from scheduling preventive maintenance to addressing urgent issues that require immediate attention. The goal is to avoid technical jargon and present actionable insights in a way that is accessible to all members of the maintenance team.
Timely Distribution of Oil Analysis Findings
Once oil analysis is complete, it’s important for the findings to be communicated quickly to ensure that any necessary actions can be taken before minor issues become major problems. Delays in reporting can lead to unexpected downtime, equipment failure, and increased maintenance costs. Therefore, the process of conveying the analysis results should be both swift and precise.
Facilitating Proactive Maintenance through Effective Communication
-
Customized Reporting: Reports should be tailored to the specific needs and knowledge levels of the maintenance personnel who will be using them. Graphics, charts, and highlighted action items can enhance understanding and readability.
-
Integrated Solutions: The use of digital tools, such as dashboards or mobile apps, can help in managing and communicating oil analysis data promptly and effectively. These tools often allow for real-time updates and alerts.
-
Training and Support: Providing training on interpreting oil analysis reports can empower maintenance staff to make more proactive and knowledgeable decisions. Support from the oil analysis provider in explaining and clarifying the reports can also be invaluable.
Training and Continued Education
Training is essential for anyone involved in the oil analysis program. It ensures that staff understand the purpose of the program, how to correctly collect samples, and how to respond to the results.
Integration with Maintenance Strategy
To maximize its effectiveness, oil analysis should be integrated into the broader maintenance strategy, working in tandem with other preventive measures.
Designating Roles and Responsibilities
For the program to run smoothly, everyone involved must know their roles and responsibilities. This clarity encourages accountability and ensures the seamless operation of the program.
Continuous Improvement and Review
The best oil analysis programs are not static—they evolve based on feedback and review. Continually looking for ways to fine-tune procedures ensures the program remains effective over time.
Vendor Relationships and Support
Building strong relationships with product and service providers, like those offering to be a fuel supplier in California, ensures you have access to quality materials and support when it comes to interpretation and action derived from analysis results.
Consistency with Industry Standards
Adhering to established industry standards for oil analysis helps validate the reliability of the program and its adherence to best practices.
Timely Service and Delivery
The prompt delivery of both samples to the laboratory and results to maintenance teams is critical in an oil analysis program. Services such as bulk fuel delivery ensure machinery keeps running efficiently while waiting for analysis results, which aids in minimizing downtime.
Applying the insights gained from oil analysis promptly is just as crucial as the analysis itself. Timely actions can prevent minor issues from developing into significant failures.
Wrapping Up
In closing, an effective oil analysis program requires thorough planning, execution, and continuous improvement. It is not merely about performing tests but about creating a comprehensive process that integrates seamlessly with the overall maintenance strategy. By considering these elements, a business can ensure the longevity and performance of its machinery through diligent monitoring and maintenance.